Fresh.Modern.Secure.
State-of-the-Art Assisted Living Facilities.
View PortfolioMorning Star Village
Rockford, Illinois.Clean.Spacious.Comforting.
State-of-the-Art Independent Senior Living Facilities.
View PortfolioGable Point Senior Living Apartments
Crystal Lake, Illinois.Open.Inviting.Ethereal.
State-of-the-Art Ecclesiastical Buildings.
View PortfolioPeace Lutheran Church
Fort Myers, Florida.Timeless.Memorable.Contemporary.
State-of-the-Art Education Buildings.
View PortfolioRockford Public Schools Administration Building Clerestory
Rockford, Illinois.Compact.Central.Adaptable.
State-of-the-Art Multi-Family Housing.
View Portfolio3rd and 11th Townhomes
Rock Island, Illinois.Dynamic.Unique.Innovative.
State-of-the-Art Design Build Facilities.
View PortfolioFlagg-Rochelle Park District REC Center
Rochelle, Illinois.
The Story Behind 1919 Architects
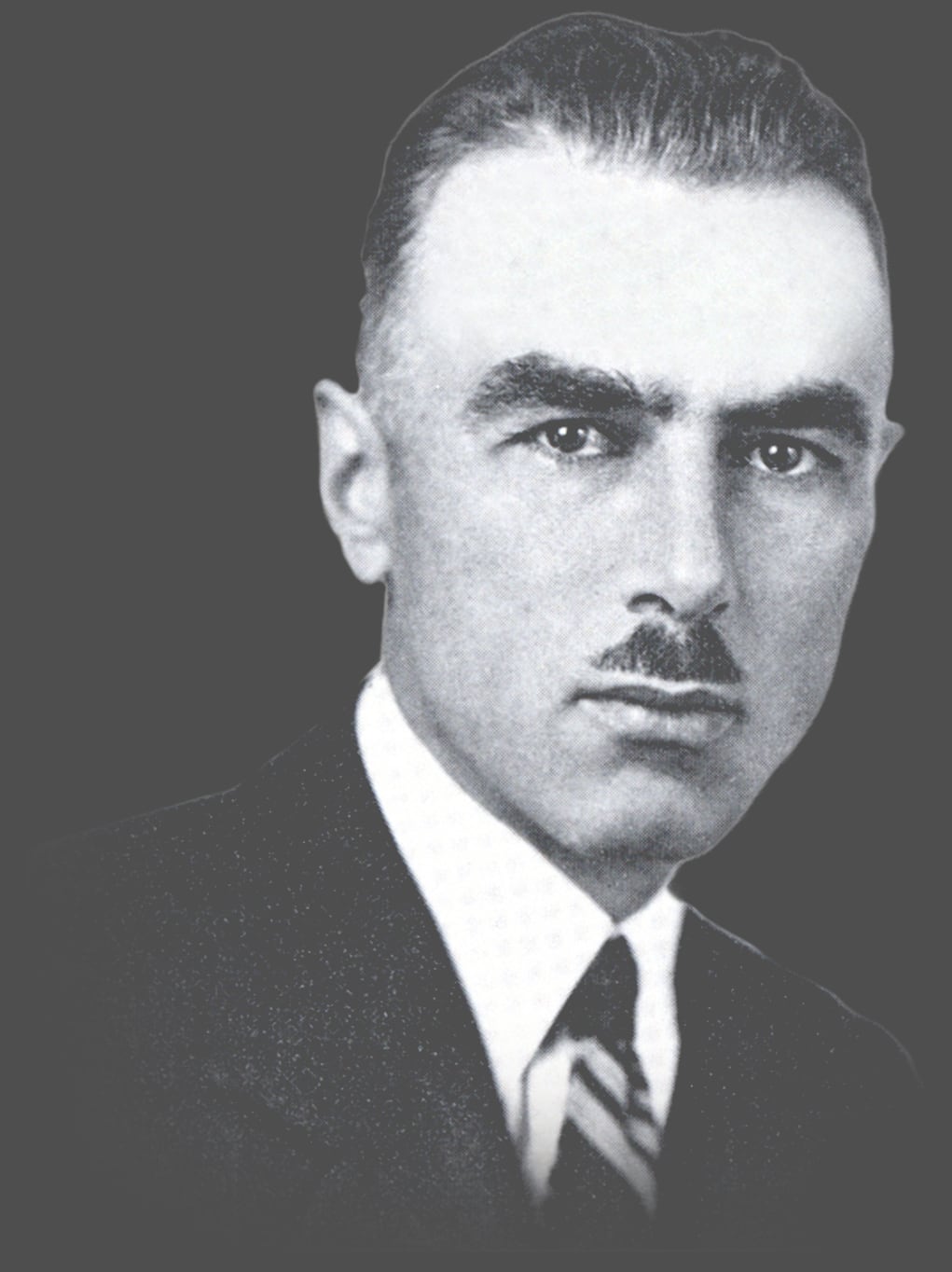
Jesse A. Barloga, Founder.
The Story Behind 1919 Architects
Beginning in 1919 as the practice of noted Northern Illinois architect, Jesse A. Barloga, our firm has flourished under the direction of five presidents since then, each contributing their own styles and philosophies to the firm’s legacy.
With over 100 years of tenure, the company has a rich history of delivering quality work. The firm completed over 150 projects for Woodward Governor, acting as their sole architect until 1979. Other projects include the Rock River News Tower, Sigma Nu Fraternity House for the University of Iowa, West High School, and various single-family homes – including the Browns Hill subdivision. During this time the firm also designed projects in Japan, the Netherlands, and England.
Our Services
1919 Architects is a full service architectural firm providing personalized service backed with quality performance.
From coordinating soil investigations to producing landscaping plans; from providing color and material selection boards to producing eye-catching 3D renderings, we surpass our competition and exceed our clients’ expectations. Our goal is to ensure that the projects run in a smooth, efficient, and cost-effective manner.
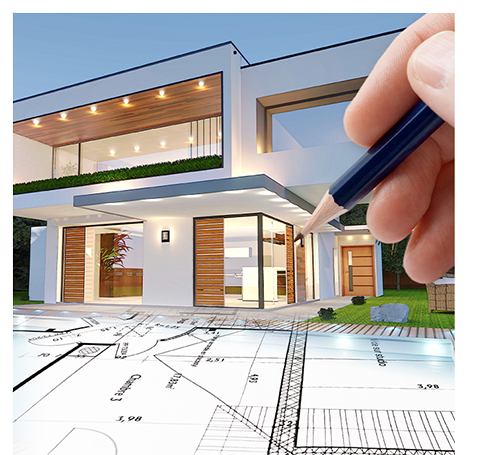
Architectural Design
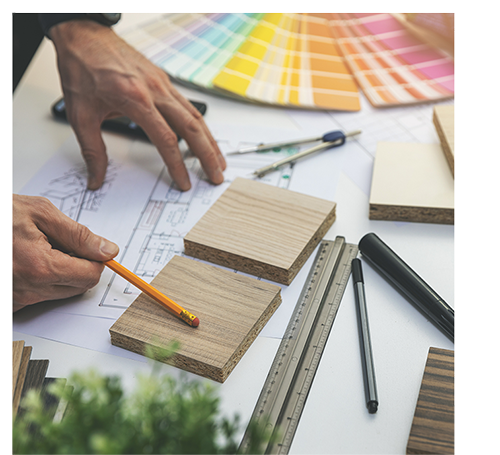
Interior Design
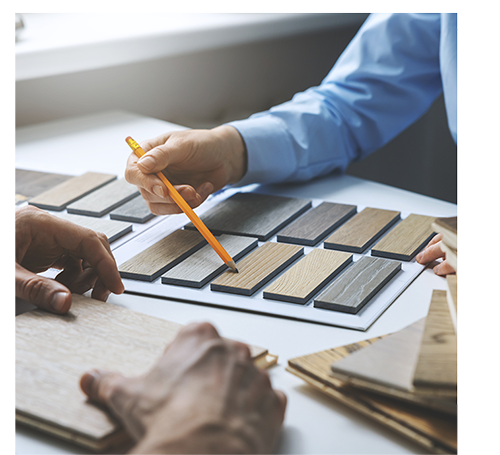
Furniture Procurement
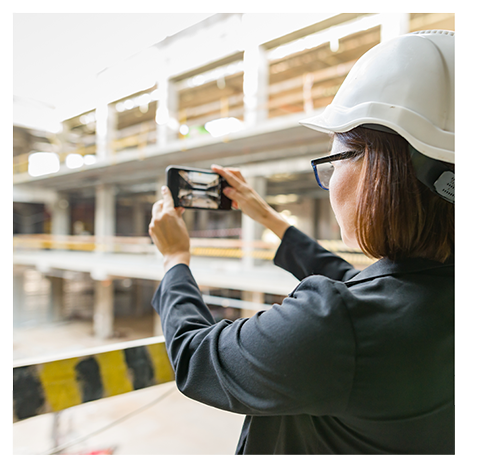
Independent Construction Observation
LICENSED FOR ARCHITECTURE IN 12 STATES — AND GROWING.
1919 Architects is licensed and active in the following areas:
Illinois
Wisconsin
Indiana
Iowa
Missouri
Kansas
Oklahoma
Texas
North Carolina
South Carolina
Florida
Arizona
Don’t see your state listed? We may be seeking opportunities to expand our licensing into other states. Call us today at any of our three office locations:
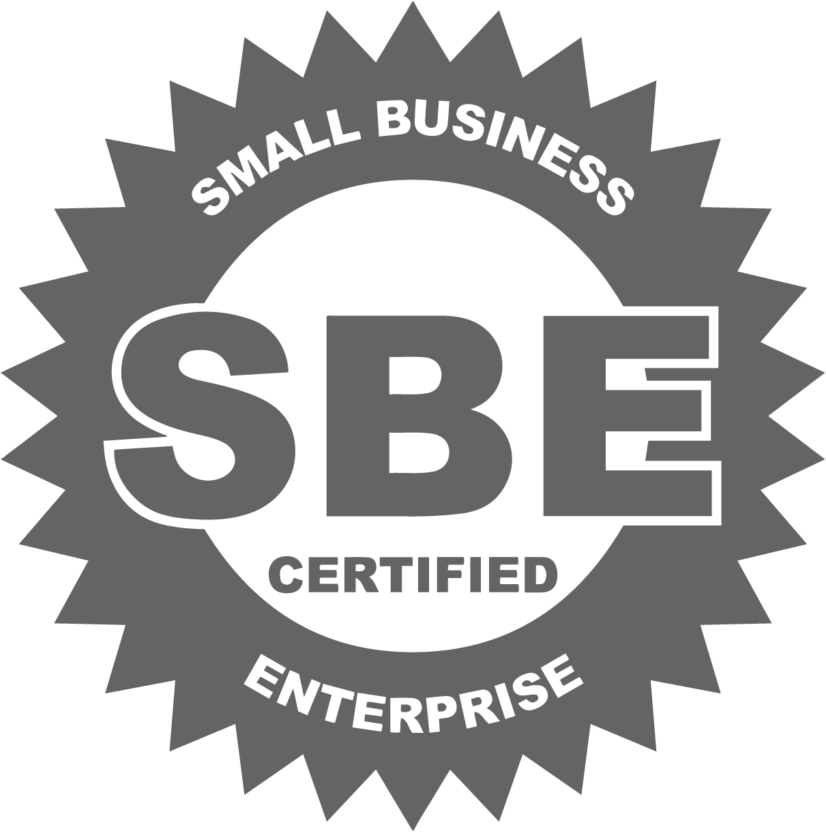
Architectural Portfolio
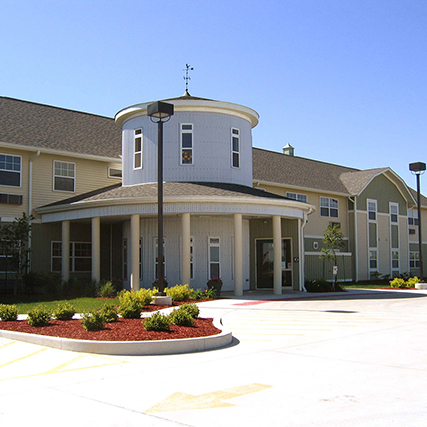
Independent Senior Living
Rolling Meadows is a 23-unit senior living apartment building built in a rural community, and designed to embrace the agricultural area. The main entry replicates a grain silo with dramatic two-story space capturing the sun at different intervals of the day. Read More
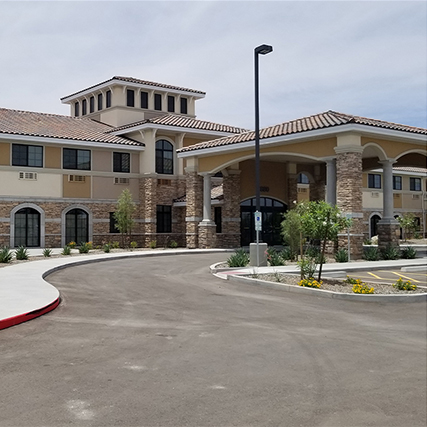
Assisted Living
The Mission at Agua Fria is a state-of-the-art Spanish style assisted living facility, located on a 7-acre campus. The facility consists of 32 assisted living and 58 memory care private residences. This 73,856 square building offers a beautiful and comfortable space for its residents. Read More
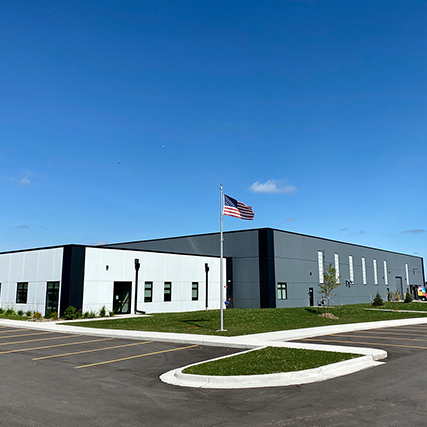
Design Build
Meridian is a 50,000 square foot design build facility located in Loves Park, IL. This project received a 2020 honorable mention from Chief Building Awards in their manufacturing-industrial category. Construction included high exposed ceilings, display area for products, and high-speed overhead doors. Read More
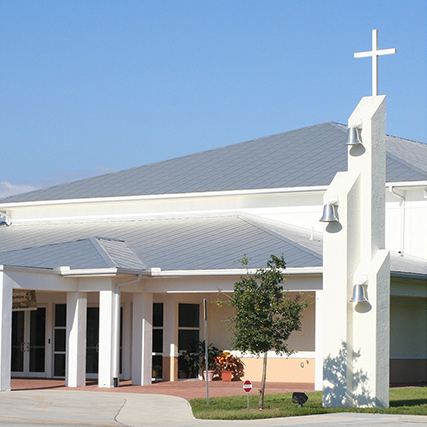
Ecclesiastical
Peace Lutheran Church in Fort Myers, Florida, features a sanctuary/fellowship hall, administrative offices, and childcare/ministries. Utilizing a more traditional Florida appearance, we incorporated standing seam metal roofs and port & cement stucco exterior. Read More
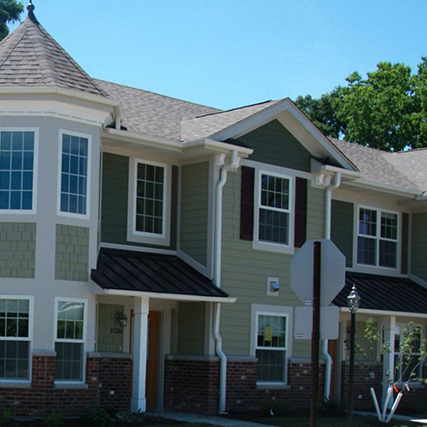
Multi-Family
The 3rd & 11th Townhomes are seven new infill townhomes consisting of four 3-bedroom and three 2-bedroom single family units. The townhomes have an open floor plan, carpeted bedrooms, and wood laminated floors in the main living area. Read More
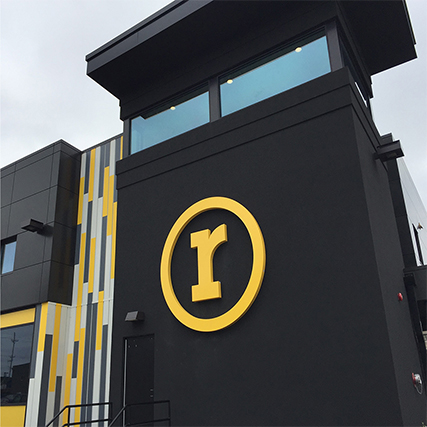
Not-for-Profit
The Rockford Rescue Mission Pitney Place Addition is a two-story, 25,000 sq. foot expansion that provides 120 additional beds to a long-term life recovery program on the 2nd floor. The ground floor of the Pitney Place also houses a bright, colorful area for children to enjoy during their stay. Read More
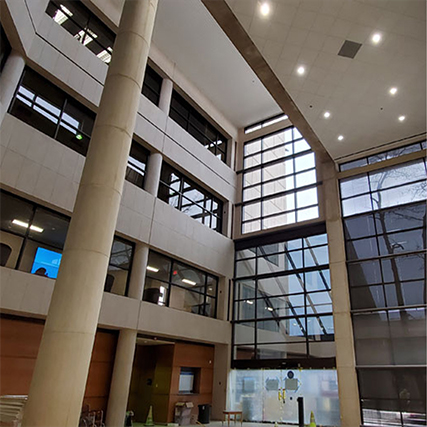
Education
We provided a new design for the clerestory located at the Rockford Public School District Administration Building. We removed the sloped glazing and designed an addition with clerestory lighting. The roofing was replaced with a new single membrane roofing system. Read More
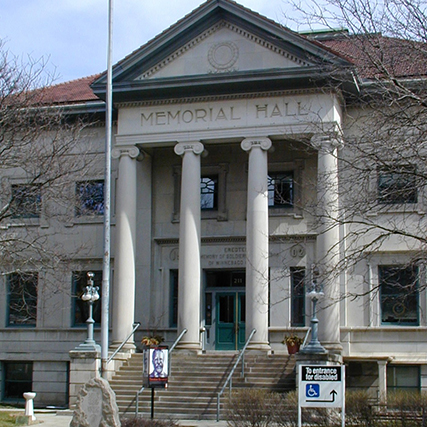
Archives
The firm completed the Veterans Memorial Hall in 1903 in conjunction with the Carnegie Library, both of which share the same classical scale and details. The hall is the first ever Memorial Hall in the nation - built in honor of the veterans of the Civil War and Spanish American War. Read More
Commercial
66,000 sq. foot grocery store featuring a coffee center, in-store bank, prepared foods area, liquor department with a reach-in beer cooler, pharmacy, full-service floral department, and full-service bakery. Read More
CUSTOMER REVIEWS
“I give Tyson and Billy Architects the highest rating available when it comes to customer service, professionalism, quality of service and understanding client’s needs. We were highly satisfied and would recommend them to friends or colleagues.”
“Ron Billy and his firm have delivered very well on the requirements of my projects over the last 25 years. He’s my ‘go-to’ architect!”
“1919 Architects, formerly known as Tyson & Billy, has been a sincere pleasure to team with on over a dozen key projects in recent years. Public and private spaces alike, the professionalism is unsurpassed! Cheers to many more.”
“Rockford Rescue Mission needed a new space where women and children could find hope and restoration. Tyson and Billy Architects worked with us to create Pitney Place, which has become a model for rescue missions across the country.”
WHAT’S NEW AT 1919 ARCHITECTS?
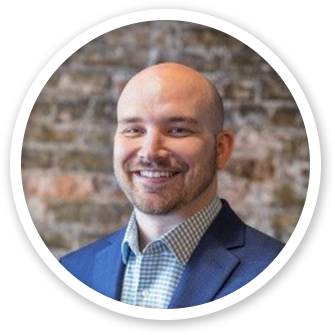
Meet Zach Enderle, AIA
Welcoming new partner and vice president to the company, Zach Enderle, AIA. Zach has a Master’s Degree in Architecture from the University of Illinois at Urbana-Champaign and is certified by the American Institute of Architects (AIA). With over a decade of experience in architecture, we are delighted to have him on our team!